KyleQ
Bronco Guru
- Joined
- Apr 24, 2008
- Messages
- 5,480
As we all know, our projects are never done, and mine is no exception. My current setup is a stock 302/C4/Atlas2 (in D20 configuration). When I installed my Atlas I ran into the Cage bracket bolts and had to flip some of them out to get the case to fit. I would have loved to clock it up another position, but my axle stretch put the Cage brackets in the way, I thought I didn't have a choice.
This summer I am going to be pulling the motor/trans/transfer case out and swapping in a NP435 and a host of other upgrades. This is a thinking out loud thread, please let me know if you would do anything differently or if I should make some changes.
My plans - front to back
My biggest annoyances revolve around my Atlas swap - I have a hard time using the twin sticks as I've got to put the C4 into neutral to shift unless I'm rolling at the perfect speed and it hangs down too low. I can't clock it due to the Cage arms, but I think I have a solution.
I want to notch the motor mount towers and turn the drivetrain towards the passenger side. This should give me the clearance I need to clock the atlas flat and get rid of the temporary skid plat I built, it hangs up on everything! I'm going to be ditching the manifolds for the fenderwell exit headers, giving me more room under the truck and, more importantly, keeping removing heat from under the truck too!
I'm thinking that angling the motor in the frame will cause fan issues, hence the move to an electric setup, I'm hoping it doesn't affect the headers and the clutch linkage much. If the clutch doesn't work reliably with the factory linkage I'll just go hydraulic sooner then planned ($$$).
This is how the Atlas fits under the Bronco - it's almost flat to the Cage brackets. My skid plate is no lower the the Cage brackets, but it's directly in the middle of the truck and gets hung up on things, it was immediately evident playing in the sand.
Has anyone ever turned the drivetrain to clear a transfer case? I can't think of any reason that this won't work... I plan on installing a 1-2" (1.5" %) ?) to help clear the eventual taller EFI 351W along with my power steering and transmission.
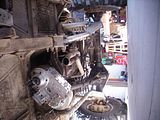
This summer I am going to be pulling the motor/trans/transfer case out and swapping in a NP435 and a host of other upgrades. This is a thinking out loud thread, please let me know if you would do anything differently or if I should make some changes.
My plans - front to back
- Replace factory fan with electric (Taurus fan, custom shroud)
- Install headers (Hooker # 9814HKR fenderwell exit)
- Install NP435 (1" spacer/V6 intermediate method)
- Clock Atlas and redesign skidplate
My biggest annoyances revolve around my Atlas swap - I have a hard time using the twin sticks as I've got to put the C4 into neutral to shift unless I'm rolling at the perfect speed and it hangs down too low. I can't clock it due to the Cage arms, but I think I have a solution.
I want to notch the motor mount towers and turn the drivetrain towards the passenger side. This should give me the clearance I need to clock the atlas flat and get rid of the temporary skid plat I built, it hangs up on everything! I'm going to be ditching the manifolds for the fenderwell exit headers, giving me more room under the truck and, more importantly, keeping removing heat from under the truck too!
I'm thinking that angling the motor in the frame will cause fan issues, hence the move to an electric setup, I'm hoping it doesn't affect the headers and the clutch linkage much. If the clutch doesn't work reliably with the factory linkage I'll just go hydraulic sooner then planned ($$$).
This is how the Atlas fits under the Bronco - it's almost flat to the Cage brackets. My skid plate is no lower the the Cage brackets, but it's directly in the middle of the truck and gets hung up on things, it was immediately evident playing in the sand.
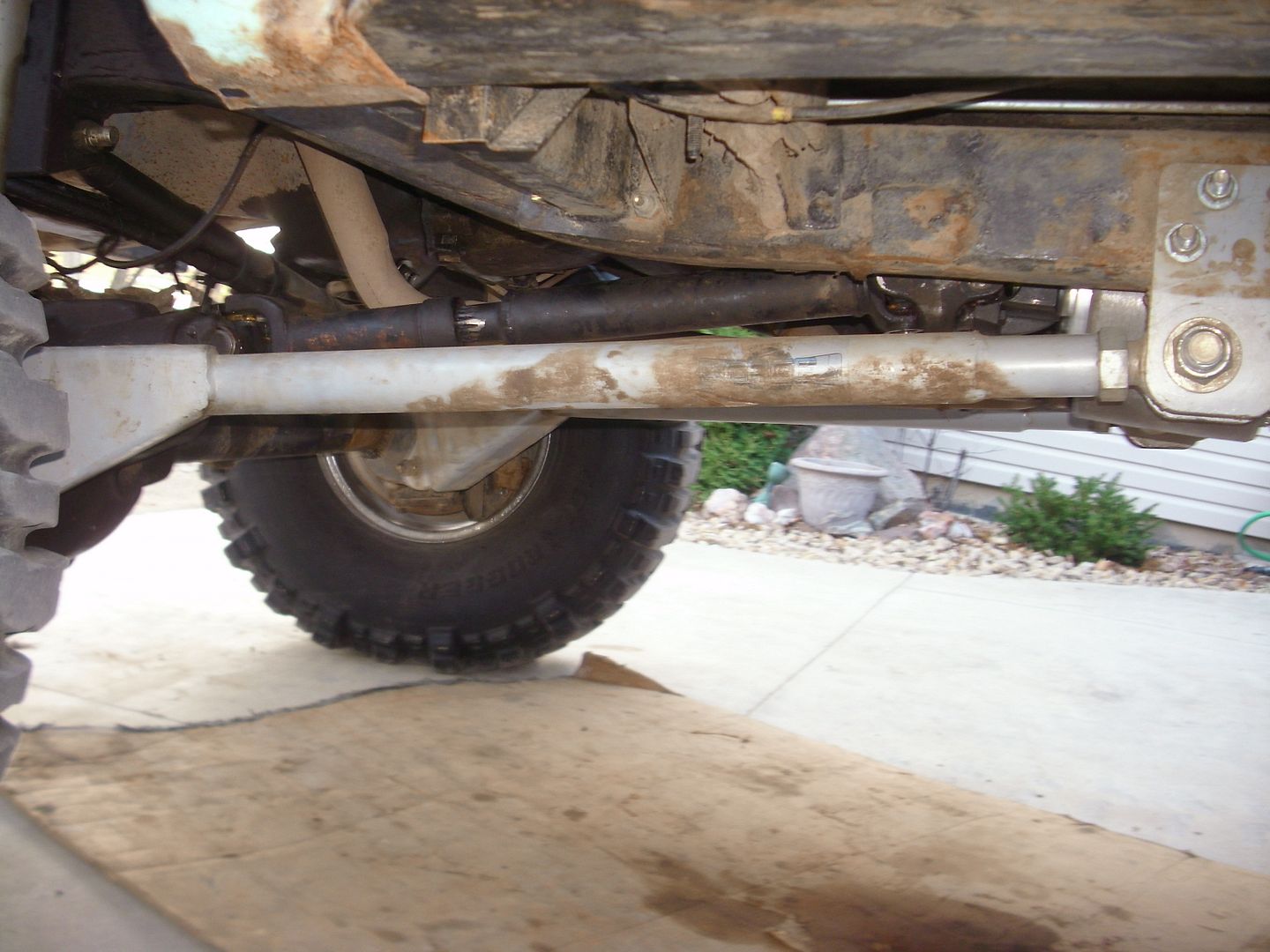
Has anyone ever turned the drivetrain to clear a transfer case? I can't think of any reason that this won't work... I plan on installing a 1-2" (1.5" %) ?) to help clear the eventual taller EFI 351W along with my power steering and transmission.