Hello,
I've just started into a new to me '68 project, which seems to have lived a very hard life. It needs a ton of work, including floor replacements, panels, etc, but the saving grace is the basic tub is nice and solid.
I'm new to metal working and welding. I've picked up a 110V Mig welder, I've been practicing a bit and I'm about ready to dig in.
I have new floor panels that I'll be installing. That seems fairly straight forward, what with all the excellent advice here. I'd like some advice on another area that needs some attention.
The hard top bolt holes in the top of the upper quarter panel are ripped and pulled. I've attached photos of two examples.
This first example is the worst one.
How should I tackle this? Cut out a nice square, weld in a patch to match and re-drill or some other approach?
The second example, is more common on this truck.
The metal around the bolt hole is raised and split. Should I open up the crack, get things fairly flat, weld the crack up then grind smooth? If another option is better I'd appreciate the advice.
Thanks in advance.
I've just started into a new to me '68 project, which seems to have lived a very hard life. It needs a ton of work, including floor replacements, panels, etc, but the saving grace is the basic tub is nice and solid.
I'm new to metal working and welding. I've picked up a 110V Mig welder, I've been practicing a bit and I'm about ready to dig in.
I have new floor panels that I'll be installing. That seems fairly straight forward, what with all the excellent advice here. I'd like some advice on another area that needs some attention.
The hard top bolt holes in the top of the upper quarter panel are ripped and pulled. I've attached photos of two examples.
This first example is the worst one.
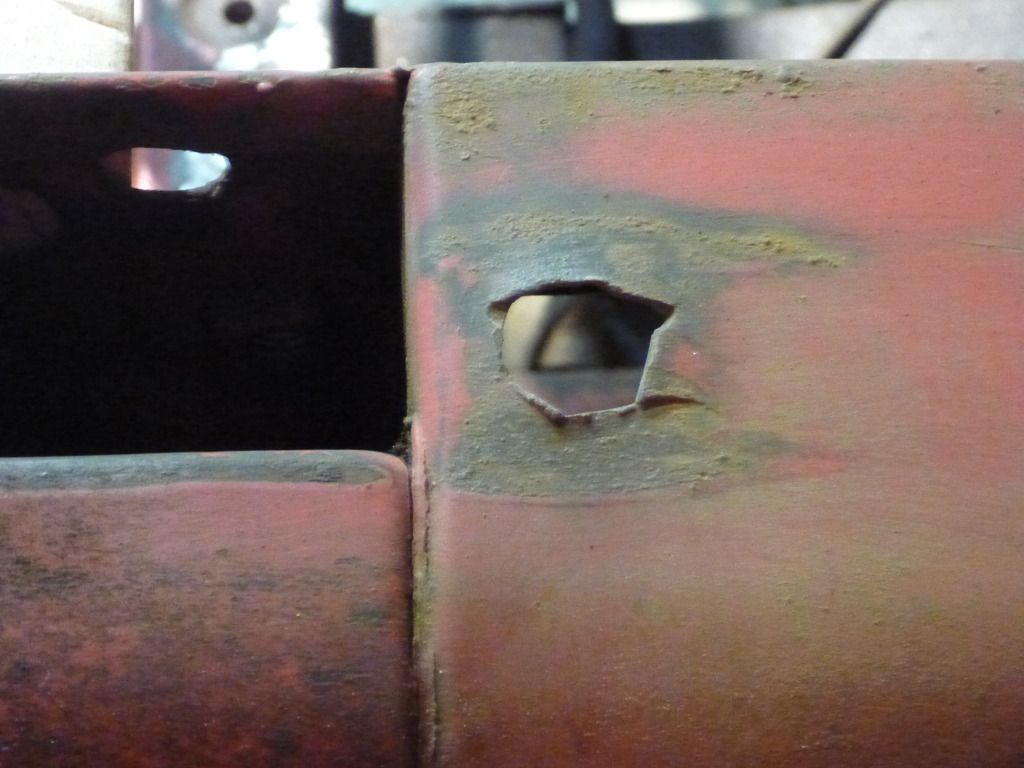
How should I tackle this? Cut out a nice square, weld in a patch to match and re-drill or some other approach?
The second example, is more common on this truck.
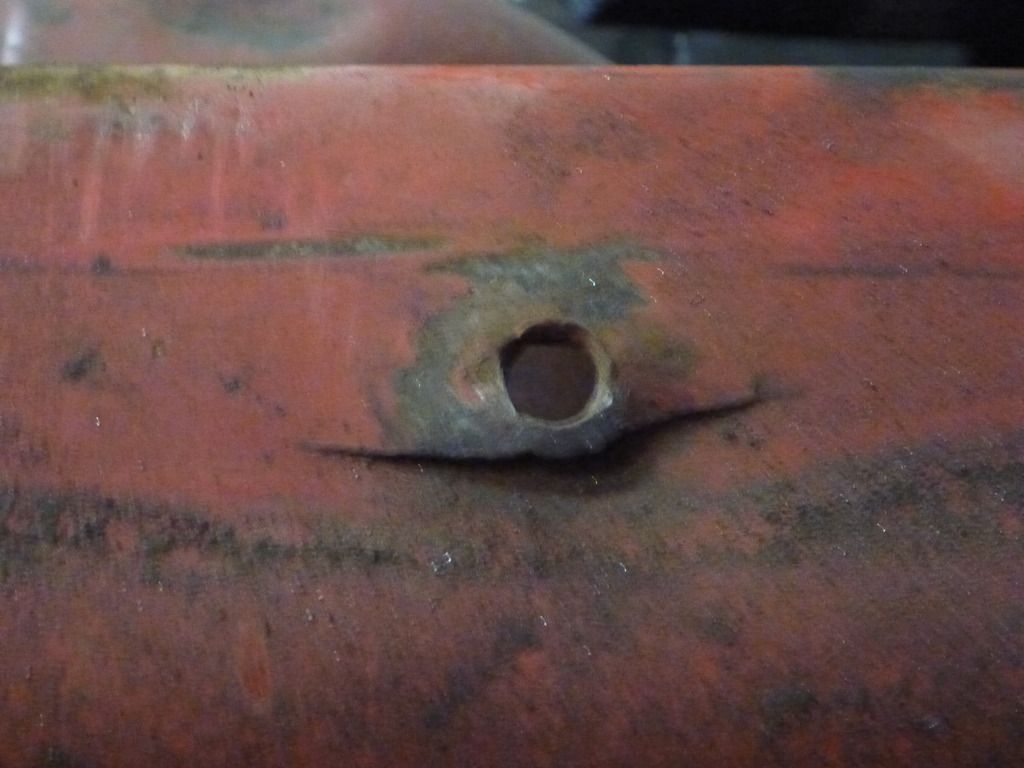
The metal around the bolt hole is raised and split. Should I open up the crack, get things fairly flat, weld the crack up then grind smooth? If another option is better I'd appreciate the advice.
Thanks in advance.