dezertbronco
Newbie
- Joined
- Sep 25, 2004
- Messages
- 50
I am welding the threaded bungs for the rod ends into the end of my radius arms, and after I finished the rosette weld and tacked the end into place I had a hard time threading the rod end into place. It went but not as easily as before I started welding.
Could the heat be warping the bung that much?
I thought welding the bung with the rod end in place would be too much heat for the rod end.
Could the heat be warping the bung that much?
I thought welding the bung with the rod end in place would be too much heat for the rod end.
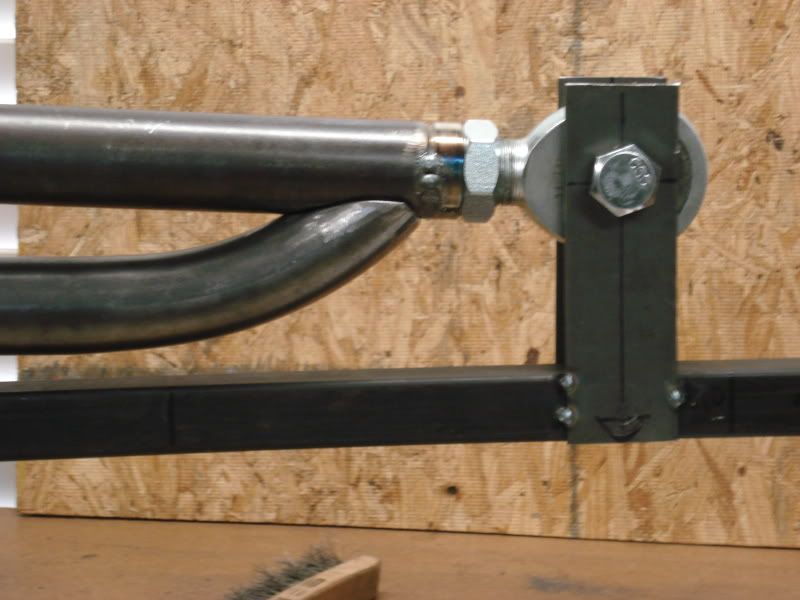
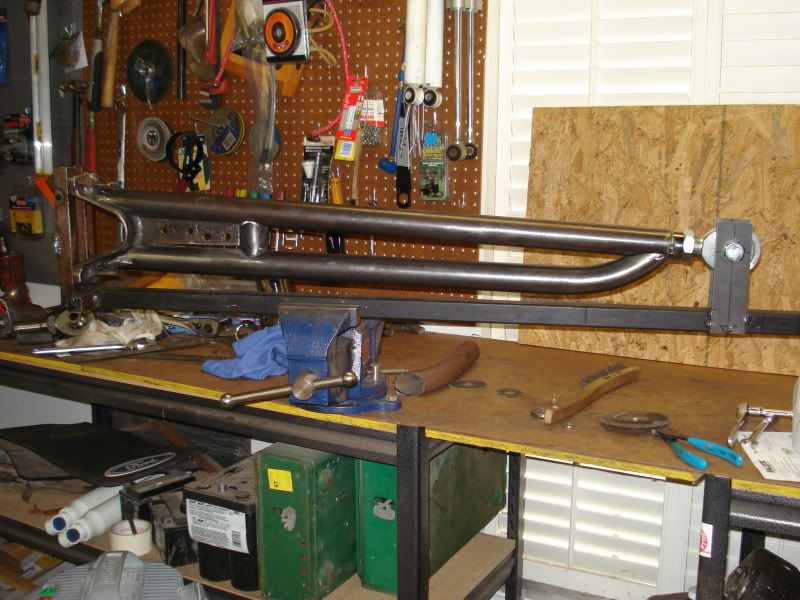