Nothing Special
Sr. Member
- Joined
- Nov 25, 2016
- Messages
- 841
A lot of work with a little to show for it. I decided the first thing to do would be to make clearance to clock the transfer case up. The Atlas 2 transfer case has 4 sets of holes for the mounting studs. Putting the studs in different holes will rotate the 'case up or down. When I first installed the Atlas I found that it had to be clocked in the lowest position to clear the frame.
That hasn't been a huge issue with the dropped radius arm mounts because it was still higher than the arm mounts. But now that I'm going to be raising the radius arms I want to get the transfer case higher. Here's an out-of-focus side view showing the current situation. The tape measure is showing 15.5" clearance under the lowest point on the transfer case.
I started off cutting as little as I thought I could get away with, then tried fitting the transfer case in with the studs moved to the second position. I kept finding where it was hitting and gnawing off a little more metal until I could fit it in position 2. Here's the hole in the frame I ended up with...
... and here are the places where more material needs to be removed if I'm going to go any higher
I don't really want to cut much higher on the frame, and I'm a little afraid that I might need to even go through the top of the flange to get to the third position. And opening up the hole more to the front would require moving the trans cross member mounting holes which gets a little challenging. (This last picture also shows the original radius arm mounting holes above the current dropped location).
On the plus side, going up one position won't require making a new trans cross member (it would have to go below the front driveshaft rather than above if I go up another step. But on the minus side, I only gained about 1/2" under the transfer case
My original plan was to finalize where the transfer case was going to end up and then reinforce the frame where I cut it before moving on to other parts of the project. But I decided to put the transfer case on hold for now. I'm not at all sure that I want to do what it will take to go up another step, so I'll get the radius arm mounts back to stock height, get the wedges cut off the axle and rotate the pinion up to see how the front driveshaft lines up. At that point I'll see if it looks like clocking the transfer case higher will gain me enough to be worth the extra work.
That hasn't been a huge issue with the dropped radius arm mounts because it was still higher than the arm mounts. But now that I'm going to be raising the radius arms I want to get the transfer case higher. Here's an out-of-focus side view showing the current situation. The tape measure is showing 15.5" clearance under the lowest point on the transfer case.
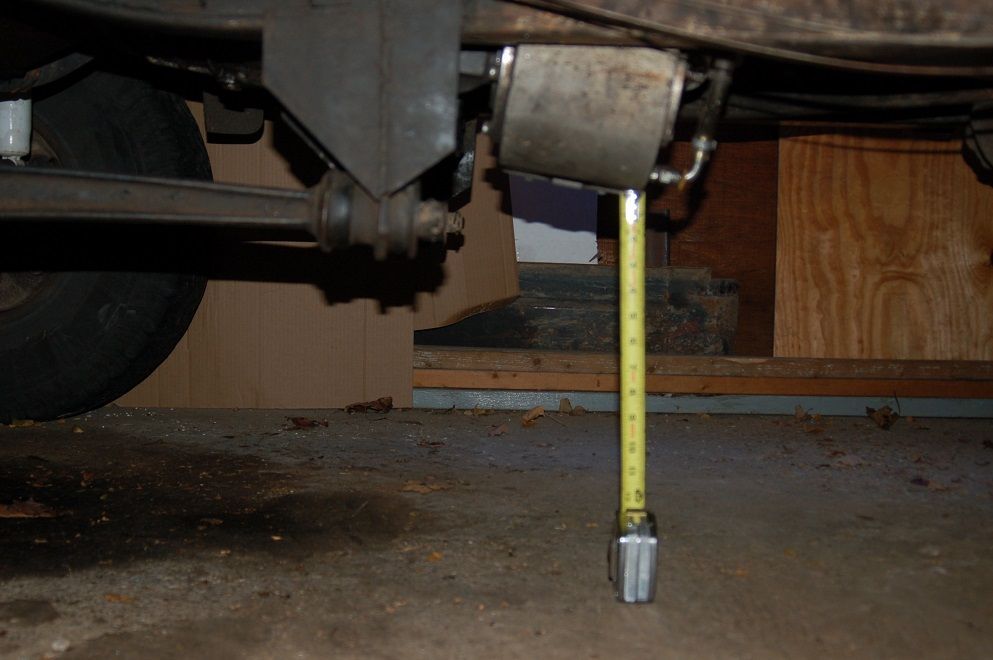
I started off cutting as little as I thought I could get away with, then tried fitting the transfer case in with the studs moved to the second position. I kept finding where it was hitting and gnawing off a little more metal until I could fit it in position 2. Here's the hole in the frame I ended up with...
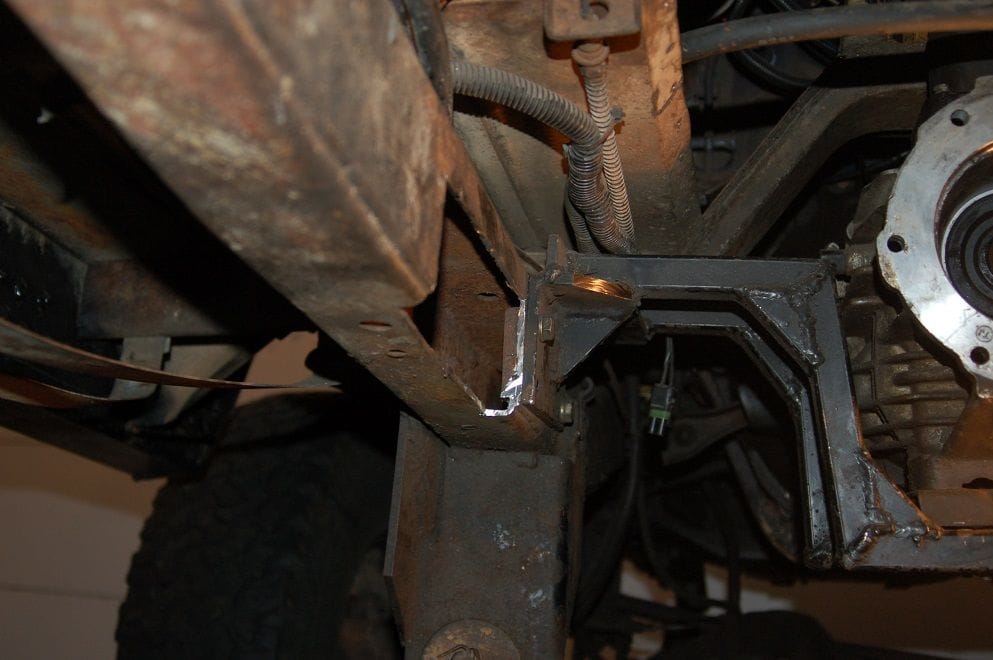
... and here are the places where more material needs to be removed if I'm going to go any higher
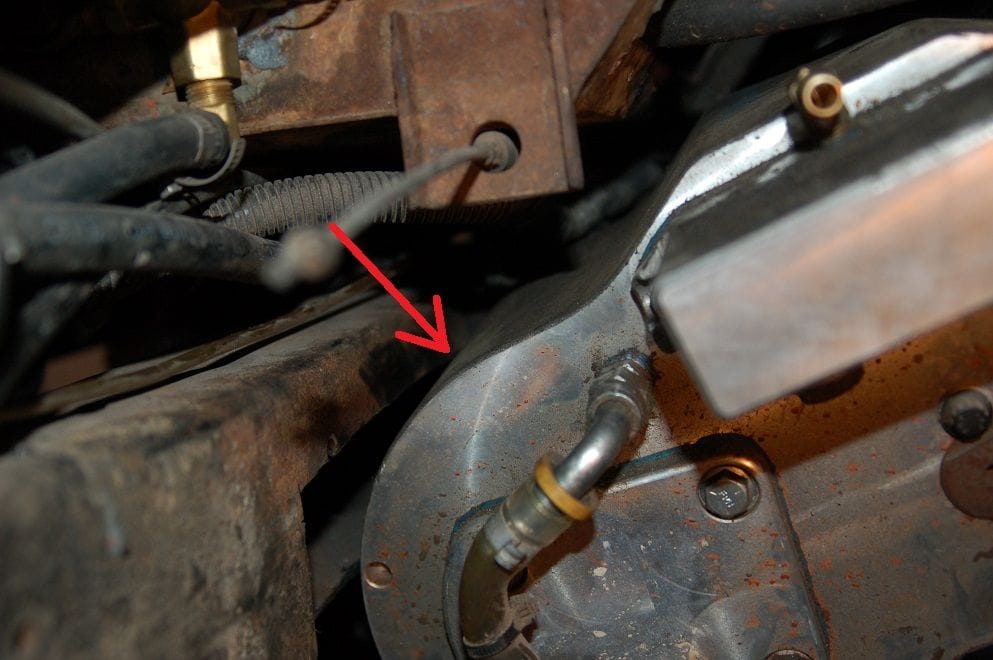
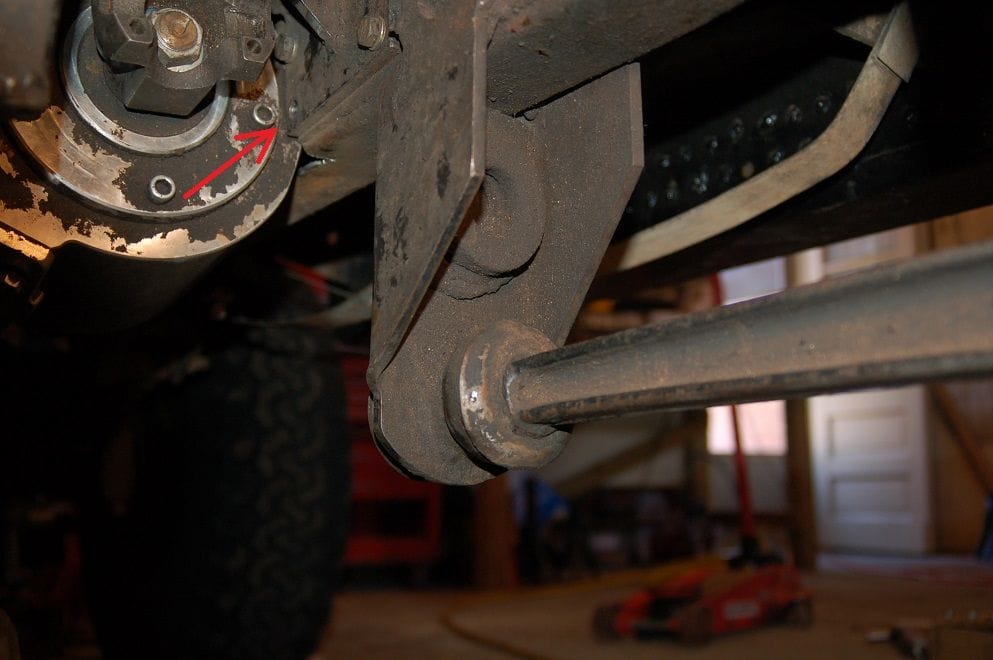
I don't really want to cut much higher on the frame, and I'm a little afraid that I might need to even go through the top of the flange to get to the third position. And opening up the hole more to the front would require moving the trans cross member mounting holes which gets a little challenging. (This last picture also shows the original radius arm mounting holes above the current dropped location).
On the plus side, going up one position won't require making a new trans cross member (it would have to go below the front driveshaft rather than above if I go up another step. But on the minus side, I only gained about 1/2" under the transfer case
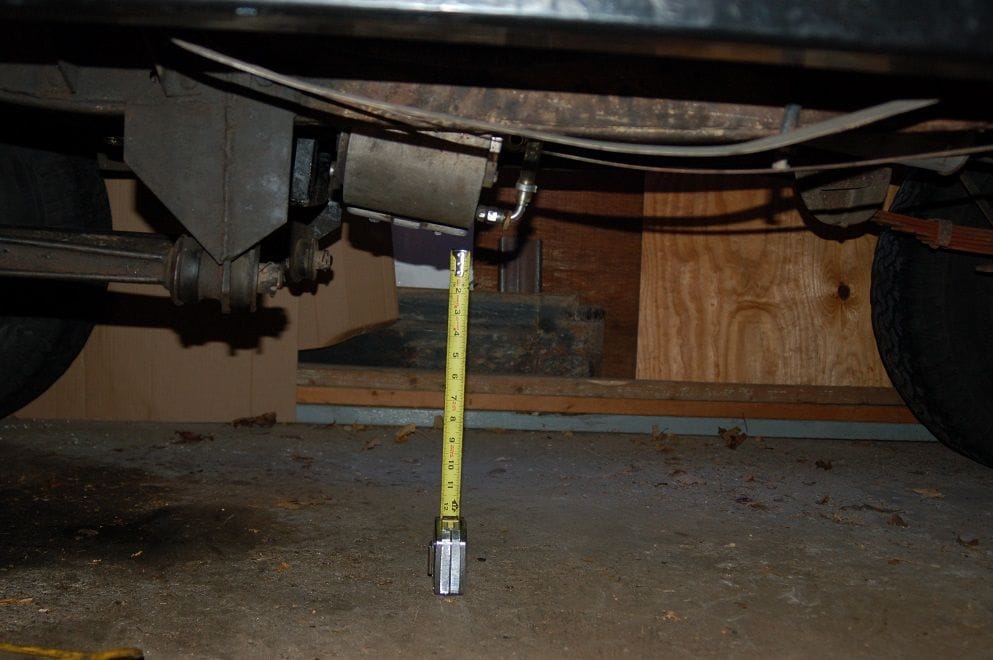
My original plan was to finalize where the transfer case was going to end up and then reinforce the frame where I cut it before moving on to other parts of the project. But I decided to put the transfer case on hold for now. I'm not at all sure that I want to do what it will take to go up another step, so I'll get the radius arm mounts back to stock height, get the wedges cut off the axle and rotate the pinion up to see how the front driveshaft lines up. At that point I'll see if it looks like clocking the transfer case higher will gain me enough to be worth the extra work.